Automotive
For many years Frost have been copper plating, copper alloy strip material, for large global Tier 1 automotive companies.
However, in an ever-demanding marketplace, pressure for cost reductions is certainly prevalent.
In order to maintain our reputation as being at the forefront of this technology, we decided to focus on reducing running & material costs significantly.
Trials were conducted within our laboratory to come up with a high-speed plating solution using conventional anode material. This increased our speed and reduced our costs as metal replenishment took place from
anodes rather than expensive
chemical salts, including those related to
copper plating.
Our Technical department also looked at wastage due to plating the full thickness of Silver where it isn’t needed.
Discussions took place with our customers to gain a full understanding of where the requirements actually were. From this, innovative methods of selective stripes, plating one side only etc.… were developed.
In other cases where the requirement was to plate all over, a method was developed to reduce the thickness distribution across the width to virtually zero, including those related to silver plating.
This innovative development was a method of ongoing measurement while the coil is moving using conventional X-ray Fluorescence (XRF). This gave us real-time readings of the complete distribution at 1mm increments to ensure no wastage or under-plating was taking place, including those related to copper plating.
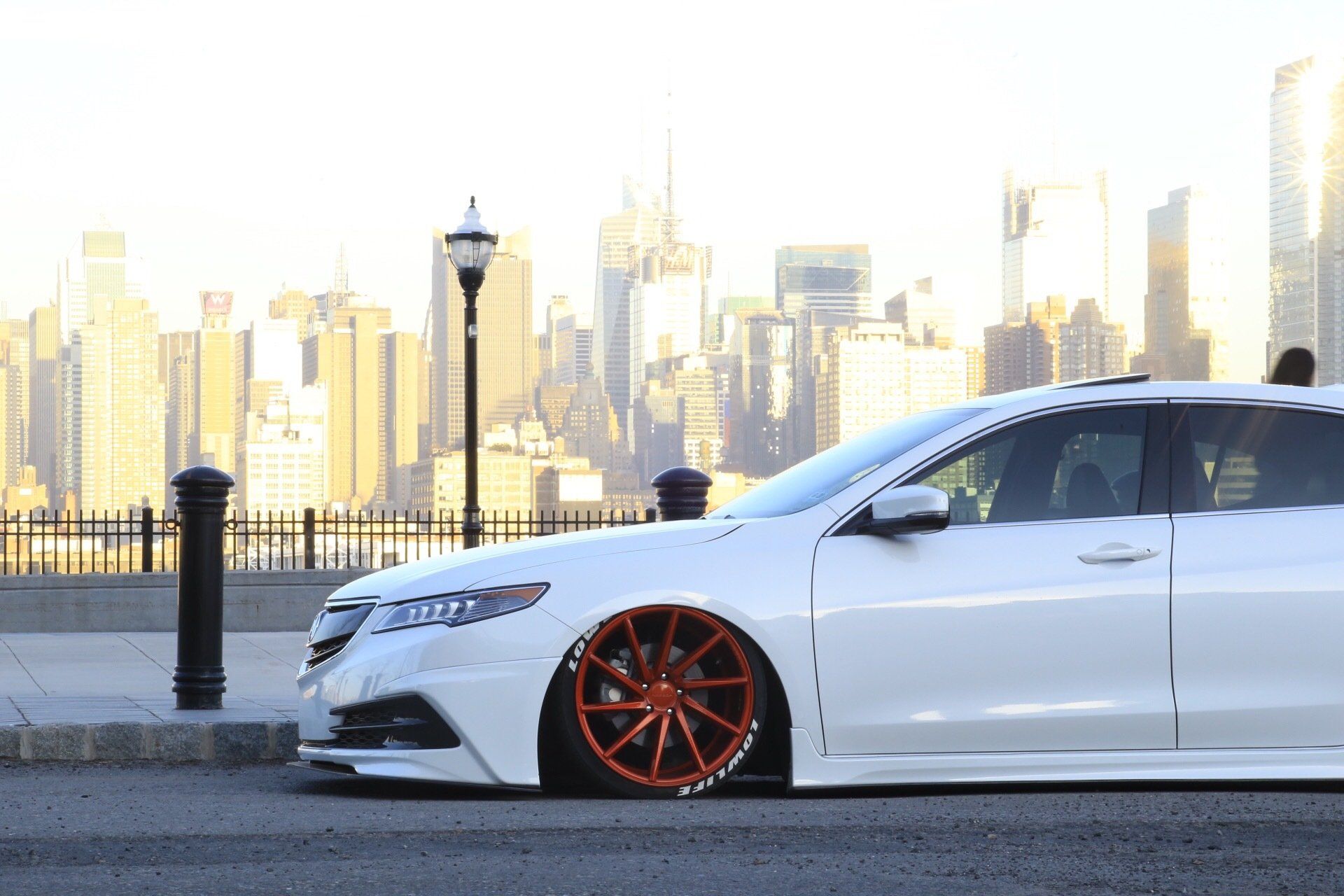
Request a free quote
If you're facing supply chain difficulties in the Automotive industry or would like to book a consultation with our experts,
contact us today for a free quote.